Valmet Automotive und Mapvision stellen Pilotanlage für eine flexible Schweißroboterzelle vor
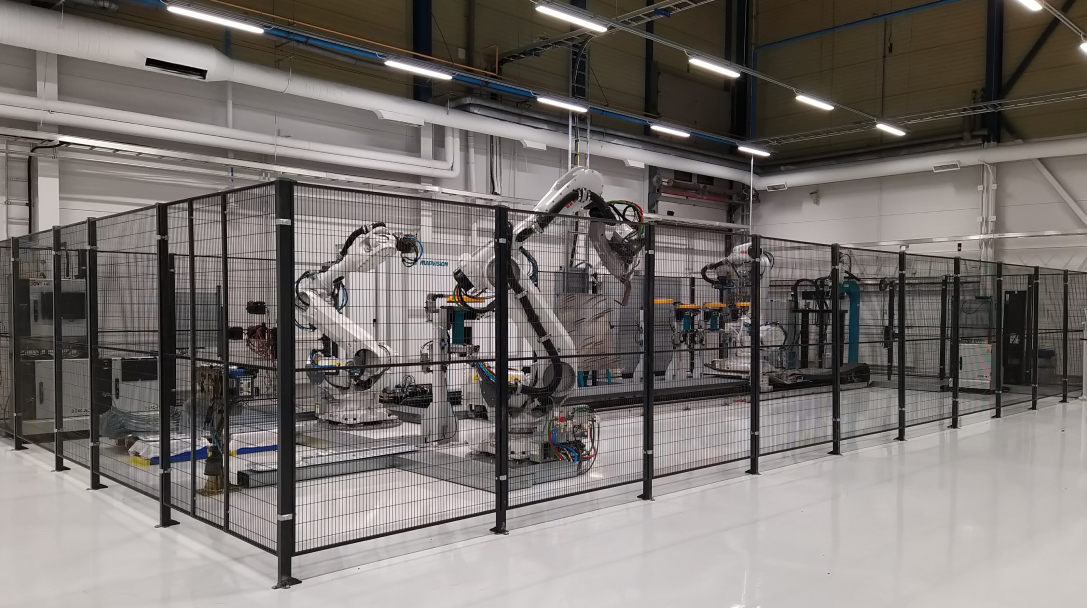
Valmet Automotive und Mapvision stellen eine flexible Schweißzelle vor, die die Automobilfertigung einen großen Schritt in Richtung eines sich selbst anpassenden Produktionsprozesses bringt. Die Pilotschweißzelle wurde heute im neuen Innovationszentrum von Valmet Automotive als Teil des Programms "Intelligent Manufacturing" des Unternehmens in Betrieb genommen.
Mit dem Programm "Intelligent Manufacturing" liefert Valmet Automotive eine Antwort auf den Wandel in der Automobilindustrie, durch den das Produktionsumfeld immer komplexer wird und Vorhersagen, z.B. zu Fertigungskapazitäten, erschwert werden. Das Unternehmen entwickelt nun Lösungen für flexiblere Fertigungsprozesse, um eine Kapazitätsoptimierung für das Automobilwerk der Zukunft zu gewährleisten.
Dazu hat Valmet Automotive im Automobilwerk Uusikaupunki ein Innovationszentrum eingerichtet, um dort künftige Lösungen zu entwickeln und zu erproben, die die Fähigkeit des Unternehmens zur gleichzeitigen Herstellung mehrerer Produkte, zur Nutzung unterschiedlicher Prozesse und zur Bedienung von Kunden mit unterschiedlichen Bedürfnissen und Anforderungen verbessern.
Im Rahmen des Programms "Intelligente Fertigung" haben Valmet Automotive und Mapvision, ihr Know-how in dem Schweißzelleprojekt zusammengeführt. Mapvision ist ein Unternehmen, das sich auf volldigitale Qualitätsmessungen auf Basis einer patentierten Multikamera-Inspektionstechnologie spezialisiert hat. Das Ergebnis ist eine Closed-Loop-Schweißzelle, die ohne herkömmliche Vorrichtungen auskommt und eine wesentlich höhere Flexibilität in der Fertigung bietet.
Im Mittelpunkt der flexiblen Schweißzelle steht die Mapvision Smart Eye Cell-Lösung, die die Multikameratechnologie und die fortschrittliche Inspektionssoftware des Unternehmens mit einer neuen flexiblen Hardware kombiniert. Die Lösung ermöglicht es den Robotern, das integrierte Inspektionssystem zu nutzen, um die Lage und Ausrichtung jedes Bauteils vor dem Schweißen zu messen und die Qualität nach jedem Prozessschritt zu überprüfen.
Das Ersetzen starrer, modellspezifischer Produktionslinien durch ein Netzwerk flexibler Fertigungszellen ist ein weiterer wichtiger Schritt für eine hochautomatisierte, effiziente Fertigung, die sich hochflexibel an die Produktionsanforderungen anpasst.
Weitere Informationen:
Matias Impivaara, Chief Growth Officer, Mapvision
Die Valmet Automotive Group ist ein führender europäischer Hersteller von Batteriesystemen für Elektrofahrzeuge und kinematischen Systemen (einschließlich Ladeklappen für Elektrofahrzeuge und aktive Spoiler) für OEMs und einer der größten Fahrzeugauftragshersteller der Welt. In der strategischen Weiterentwicklung fokussiert sich die Valmet Automotive Group auf Elektromobilität mit Entwicklung und Fertigung von Batteriemodulen sowie kompletter Batteriepacks für elektrifizierte Fahrzeuge. Die Aktivitäten in der Gruppe gliedern sich in die drei Business Lines Manufacturing, EV Systems und Roof & Kinematic Systems. Seit der Gründung im Jahr 1968 hat Valmet Automotive im Werk in Uusikaupunki/Finnland mehr als 1,7 Millionen Fahrzeuge produziert. Valmet Automotive betreibt in Finnland zwei Batteriefabriken an den Standorten Salo und Uusikaupunki. Ein drittes Batteriewerk in Kirchardt, Deutschland, geht im Jahr 2022 in Betrieb. Das Unternehmen hat Standorte in Finnland, Deutschland und Polen. Die größten Anteilseigner an der Valmet Automotive Group sind die staatliche finnische Investmentgesellschaft Tesi und die Pontos Group mit einem Anteil von je 38,46 Prozent. 23,08 Prozent werden von der chinesischen Contemporary Amperex Technology Limited (CATL) gehalten, weltweit führender Hersteller von Batteriezellen für Elektrofahrzeuge.
Mapvision ermöglicht die Zukunft der Fertigung, indem das menschliche Auge bei der Qualitätsprüfung überflüssig wird. Die 100 % x 100 %-Inspektionslösungen von Mapvision bieten die schnellsten Inline-Qualitätsprüfsysteme für komplexe Komponenten. Wir bieten eine vollständig digitale und absolute Messung aller Merkmale aller Teile in Echtzeit, und unsere fortschrittlichen Analyselösungen machen Qualitätsdaten von der „Shop Floor“ zur „Top Floor“ leicht verständlich. Wir sind die Augen intelligenter Fabriken.